What is fused deposition modelling?
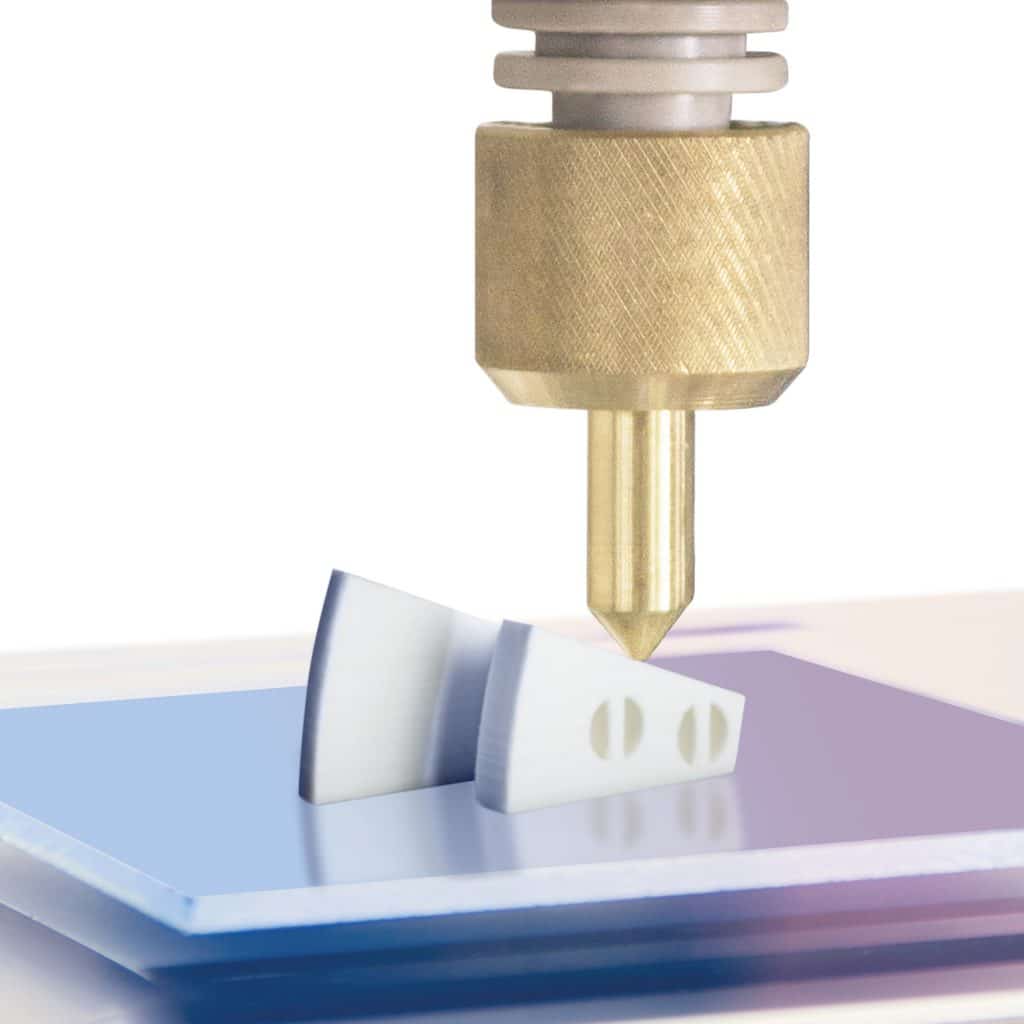
About fused deposition modelling
There are two most widely-used types of 3D printer, one being the much-used fused deposition modelling (FDM), or fused filament fabrication (FFF), printer. FDM is an additive manufacturing technique that is a cousin of the material extrusion procedure. In simple terms, it is a method whereby melted material is deposited according to the desired 3D shape and creates the predetermined object layer by layer. The materials used in this process are mainly thermoplastics and are used in filament form.
FDM is the most-used 3D print method and as such, is a method to which most beginners are exposed as a pioneering approach to 3D printing.
The process of fused deposition modelling
- The polymer filament spool is loaded into the printer and gently heated. Once the desired temperature is reached in the nozzle, the filament is fed through the nozzle, melting as it does.
- The end plate which holds the extrusion head is attached to a 3-axis system: X, Y and Z. The narrow nozzle extrudes the polymer in very thin strands along the predetermined path, the plastic solidifies upon landing on the printer base or build platform. This solidification process can be accelerated by the use of fans in the print area.
- When the shape requires that a space by filled, multiple strokes are made by the extrusion head to effectively ‘colour in’ the area. As with a domestic ink printer the machine moves as the layers are completed and more extrusion is added to fill a part before moving onto the next piece.
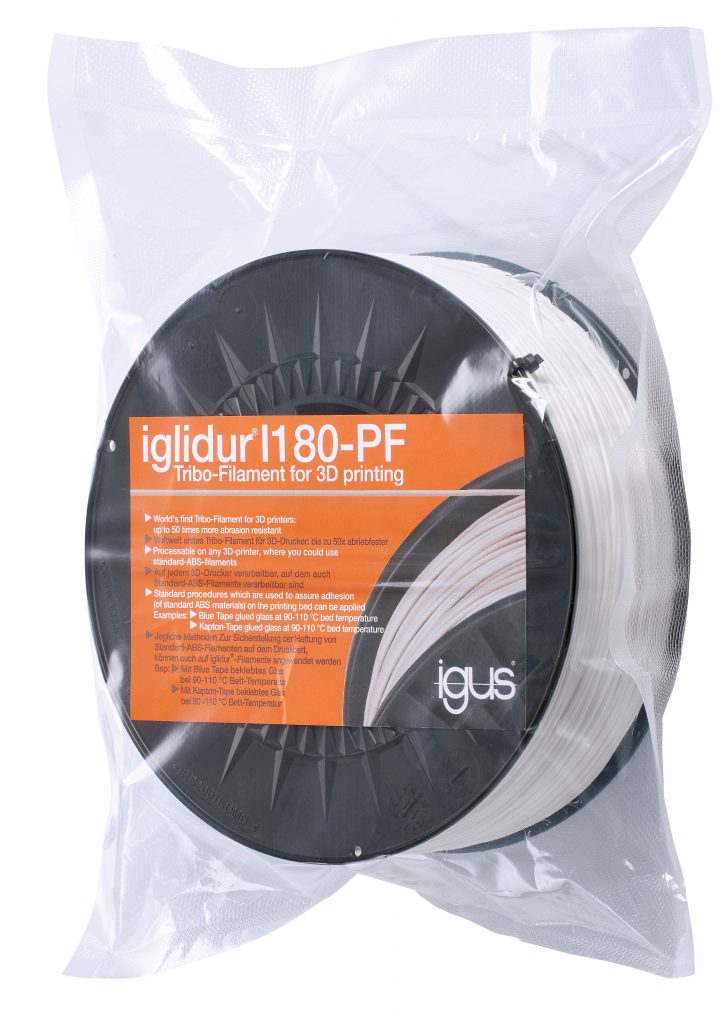
Printer adjustments
The parameters of FDM printers can be adjusted to ensure the best setting is applied to each process. In most fused deposition modelling printers, this includes nozzle and build platform temperature, speed of the build, layer height, and cooling or fan speed. Often set by the operator, although not all FDM designs allow for adjustments, it’s important that you are aware of the differences between printer brands.
Read more about 3D printing at igus® here
The printer designers are, however, definite when parametrising the layer height and build size of their FDM printer:
Build size
A typical desktop printer has a build size of 200 x 200 x 200mm, whereas industrial versions can reach 100 x 1000 x 1000mm. If more flexibility is required and cost is an important factor, then a large model can be purchased in component form and assembled upon delivery.
Layer height
A standard layer height in an FDM printer is between 50 and 400 microns, with the most common height being 200 microns. These heights can be specified upon placing an order, which is beneficial depending on the desired effects of the product. As expected, a smaller layer height produces smoother parts and higher accuracy when dealing with more complex or curved geometry; conversely, a larger layer height produces parts at a lower cost and faster than the former.
Issues with fused deposition modelling parts
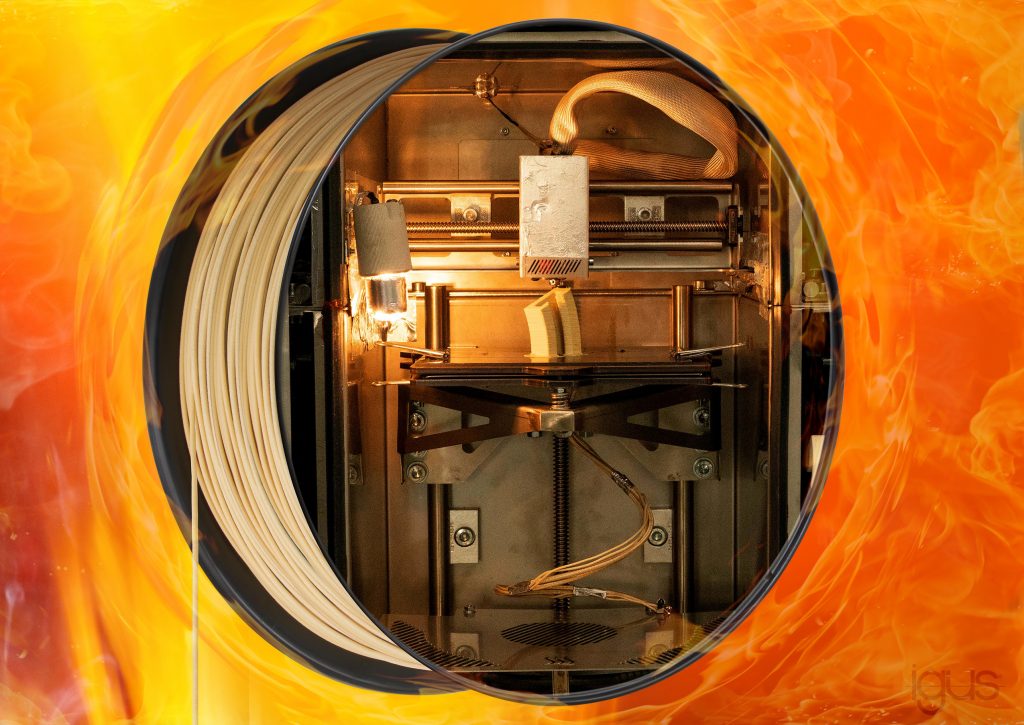
In light of the above, there are some limitations to be aware of when selecting FDM over alternative 3D print methods. Firstly, due to necessary layer adhesion, FDM parts are not isotropic, which is due to their inherently low dimensional accuracy in comparison to other 3D print methodologies. Moreover, the visible layer lines make it difficult to achieve high resolution, and in turn this produces a surface which often requires secondary finishing to reach a smooth appearance.
Benefits of fused deposition modelling parts
There are some strong advantages for choosing FDM as a 3D print method, not least for the fact it is the most cost-effective choice for 3D printing bespoke thermoplastics as parts or prototypes. Also, since the process is so fast and FDM technologies are in abundance, the lead times are considerably reduced. In addition, the materials available as thermoplastics are very wide-ranging, which makes products from this method suitable to be used not only as prototypes but also as industrial parts.
The FDM filaments available from igus® provide up to 50 times more abrasion resistance than alternative materials, and in this way offer low coefficient of friction and favourable wear behaviour. This also ensures high durability and long-lasting features which are essential when using these materials in industrial applications.
Visit the website to find out more about igus® 3D print.
Alternatively, contact our Product Manager Dean Aylott: daylott@igus.co.uk for any 3D Print enquiries.